Evaluation of the Atlantis Abutment in Implant Restoration
Lee M. Whitesides, DMD, MMSc
In treatment planning a patient, the dentist must consider many factors, including the existing pathology, the needs and desires of the patient, the materials available, the financial burden the patient must incur to receive the treatment, and the limitations and knowledge base of the dentist delivering care. Possibly the most limiting of these factors may be the knowledge base of the dentist, because that is what creates the comfort zone in which the dentist practices dentistry.
For many years, dental implants have been “outside the comfort zone” of many restorative dentists because of the variability and complexity of the restorative process.1 In an effort to simplify the process and lessen the complexity and cost of restoring dental implants, most implant companies manufacture stock abutments for their dental implants. Although generally considered simpler and less expensive than custom abutments, stock abutments have limitations which may compromise the integrity of the restoration or the esthetic result.2-5
In 1996, Atlantis Components, Inc (Cambridge, MA) developed a patented integrated computer-aided design/computer-assisted manufacturing process to fabricate patient-specific, precision-milled abutments from single blocks of titanium (Figure 1).6 Atlantis abutments are restored with traditional crown-and-bridge techniques, thus permitting the dentist unfamiliar with dental implants to easily incorporate implants into the patient’s treatment plan without venturing outside his or her comfort zone.
The following case study demonstrates the ease of restoring a dental implant using the Atlantis abutment.
Case Report
The patient was a 36-year-old woman who lost tooth No. 30 secondary to caries approximately 6 months before implant placement. After an initial consultation, the patient underwent placement of a single implant fixture (Figure 2) (Zimmer Dental, Carlsbad, CA). A surgical index was taken using Imprint™ bite (3M™ ESPE™, St. Paul, MN) with the fixture mount serving as an index tool at the time of surgery (Figure 3). A healing abutment was placed and the implant was allowed to integrate for 5 months. Postoperatively, the patient was placed on antibiotics and analgesics for 5 days. The patient returned for visits at 7 days and 21 days postoperatively for observation.
After 5 months of integration, full upper and lower arch impressions were made using polyvinyl siloxone impressions (Impregum™ Penta™ Soft, 3M™ ESPE™). After suitable impression, index, and interocclusal registrations were obtained, Atlantis Components fabricated two patient-specific, precision-milled abutments.
At the next patient visit, the surgeon removed the healing abutment, placed the Atlantis abutment into the implant, and torqued it to 30 N/cm2 (Figure 4). A provisional restoration matched to the nearby teeth for shade and adjusted slightly out of occlusion was adhered to the abutment with temporary cement (Figure 5).
The patient was referred back to her general dentist for fabrication of the final restoration. A corresponding duplicate abutment was forwarded to the restorative dentist on the cast. The restoring dentist did not need to make additional impressions and sent the unmodified duplicate abutment and cast to the laboratory with instructions for fabrication of the final restoration. The final restoration was delivered to the general dentist for final cementation (Figure 6).
Discussion
The barriers to the incorporation of dental implants into most treatment plans are primarily educational and financial. A general dentist may consider the dental implant outside of his or her comfort zone because of insufficient knowledge of dental implant techniques to appropriately treatment plan the case, place the fixture, or restore the dental implant. Additionally, the general dentist may be wary of unanticipated costs with respect to the time and/or materials involved.1,7
The simplicity, precision, and accuracy of Atlantis abutments minimize the financial burden to the restorative dentist by increasing the predictability of the restorative process while decreasing the involved chairtime.1-3,5 Because the Atlantis abutment is restored with traditional crown-and-bridge techniques, its restoration is well within every dentist’s comfort zone.
The duplicate abutment, which is unique to Atlantis Components, saves the restorative dentist additional chairtime because it can be used as a die by the laboratory to fabricate the final restoration, eliminating additional impressions. If modifications to the duplicate abutment need to be made, the laboratory uses the modified abutment for the final restoration. The patient has a suitable abutment to support the provisional while the final prosthesis is fabricated. This flexibility permits the dentist to save chairtime and materials and may increase patient acceptance of the entire procedure because minimal impressions are required.
CONCLUSION
The incorporation of dental implants into a treatment plan is often omitted because of educational and financial barriers. Use of the Atlantis abutment helps remove these barriers by providing the restorative dentist with an exceptionally high degree of final restoration predictability while decreasing the chairtime and required armamentarium of the materials involved in the restorative process.
References
1. Osorio J. Use of the Atlantis Abutment in restorative practice speeds time to function and aesthetics. Dent Implantol Update. 2000;11(8): 57-62.2. Ganz SD. Computer-milled patient-specific abutments: incredible quality with unprecedented simplicity. Pract Proced Aesthet Dent. 2003;15(Suppl 8):37-44.
3. Kerstein RB, Castellucci F, Osorio J. Ideal gingival form with computer-generated permanent healing abutments. Compend Contin Educ Dent. 2000;21(10): 793-802.
4. Schneider A, Kurtzman GM. Computerized milled solid implant abutments utilized at second stage surgery. Gen Dent. 2001;49(4):416-420.
5. Priest G. Virtual-designed and computer-milled implant abutments. J Oral Maxillofac Surg. 2005;63(9 Suppl 2):22-32.
6. Kerstein RB, Osorio J. Utilizing computer-generated duplicate titanium custom abutments to facilitate intraoral and laboratory implant prosthesis fabrication. Pract Proced Aesthet Dent. 2003;15(4):311-314.
7. Beaty KD, Steele DL, Garfield RE, et al. What measures are needed to reduce the costs of implant treatment so as to render it more affordable for the average-income patient and generally increase the demand for care? Intl J Oral Maxillofac Implants. 2003;18(6):915-921.
Figure 1 The Atlantis abutment was created by a patented integrated CAD/CAM process to fabricate patient-specific, precision-milled abutments from single blocks of titanium. | Figure 2 The patient underwent placement of a single implant fixture. | |
Figure 3 A surgical index was taken with the fixture mount serving as an index tool at the time of surgery. | Figure 4 The Atlantis Abutment placed into the implant and torqued to 30 N/cm2. | |
Figure 5 A provisional restoration adjusted slightly out of occlusion was adhered to the abutment with temporary cement. | Figure 6 The final restoration after try-in and final cementation. | |
About the Author | ||
Private Practice limited to Oral & Maxillofacial Surgery and Implant Dentistry Atlanta, Georgia |
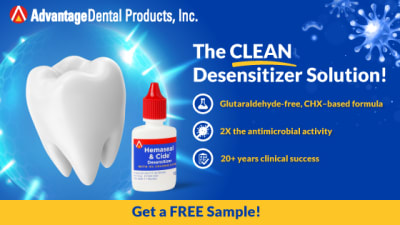