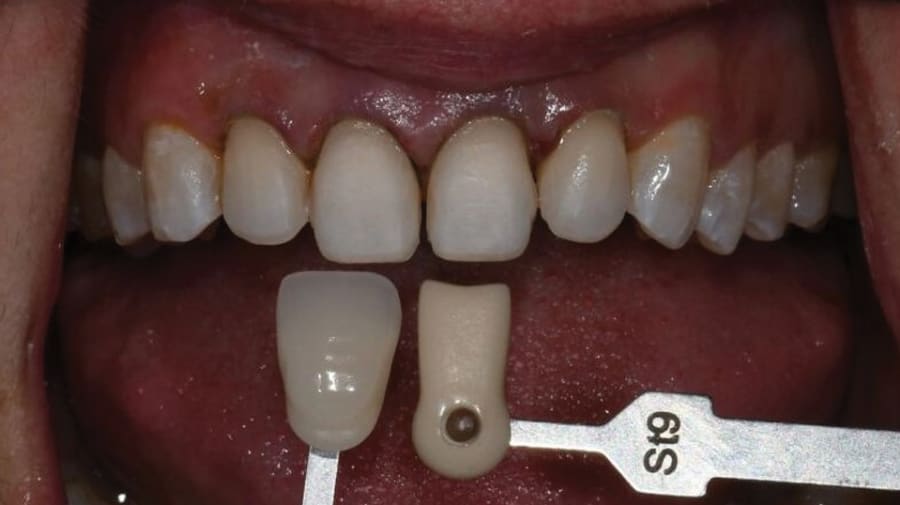
False
Advertisement
Continuing Education
Latest Courses
Current Implant Maintenance Protocols and Their Significance
Nathan E. Estrin, DMD, MS; Jon B. Suzuki, DDS, PhD, MBA; Diana Bronstein, DDS, MS; and Georgios Romanos, DDS, PhD, Prof Dr med dent
CE Credits: 2
Cost: $16.00
Antimicrobial Use in Implant Therapy: Is It Necessary?
Stefan Radovic, BSc; and Aviv Ouanounou, BSc, MSc, DDS
CE Credits: 2
Cost: $16.00
Eight Keys for the Reconstructive Therapy of Peri-Implantitis-Related Intrabony Defects
Robert A. Levine, DDS; Alberto Monje, DDS, MS, PhD; Muhammad H.A. Saleh, BDS, MSD, MS; Debora R. Dias, DDS, MSc; Khushboo Kalani, DDS, MS; Harold M. Pinsky, DDS; Jeffrey Ganeles, DMD; Franck Renouard, DDS; and Maurício G. Araújo, DDS, MSc, PhD
CE Credits: 2
Cost: $16.00
Courses by Topic
View More CoursesLatest Webinars
Compendium's Complex Cases: Hiring and Retaining an Ideal Dental Team in 2025
Irina Dragan, DMD, DDS, MS; David Alexander, BDS, MSc, DDPH; Amy Morgan, BFA
CE Credits: 1
Cost: $0.00
IV Sedation Dentistry: What It Can Do to Elevate Your Practice
John Roberson, DMD and Jay B. Reznick, DMD, MD
CE Credits: 0.5
Cost: $0.00
Peri-Implant Disease: Illuminating Laser vs. Traditional Treatment
Kevin Suzuki, DMD
CE Credits: 1
Cost: $0.00
Webinars by Topic
View More WebinarsLatest News
False
Advertisement